Recyclage de l'huile et des lubrifiants réfrigérants grâce à des séparateurs d'huile étrangère, des chariots d'aspiration et de filtration
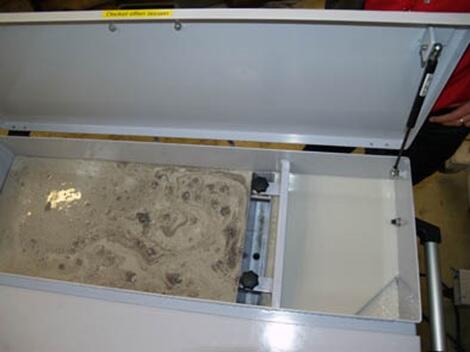
(Sulzbach-Laufen/Monheim) Parce que le filtrage et le nettoyage du lubrifiant réfrigérant est une opération coûteuse et chronophage, elle est souvent repoussée à plus tard. De même, l'accès difficile aux machines et aux centres d'usinage empêche l'entretien et le traitement réguliers nécessaires. Chez kocher-plastik, on mise depuis quelque temps sur les systèmes d'entretien et de préparation de MKR Metzger. Les opérations sont ainsi si simples et rapides que les collaborateurs les effectuent volontiers. L'homme, la machine et la qualité des pièces fabriquées en profitent.
"Ce qui était auparavant compliqué et fatigant et prenait presque une demi-journée est aujourd'hui réalisé en 20 à 30 minutes", assure Jens Bauer, chef du département de fabrication CNC chez kocher-plastik Maschinenbau GmbH. Le fabricant de machines de remplissage spéciales a obtenu cette amélioration presque inimaginable lors du traitement et de l'entretien des lubrifiants réfrigérants grâce à un chariot d'aspiration et de filtrage haute performance et à un séparateur d'huile étrangère mobile de MKR Metzger. Les deux appareils nettoient les lubrifiants réfrigérants (KSS) et les huiles de coupe directement sur la machine et les préparent pour la suite de l'exploitation. Cela ne fait pas seulement du bien à la santé des opérateurs et aux machines, cela permet également de prolonger la durée de vie des outils et d'obtenir des résultats de travail précis plus longtemps. La manipulation et l'utilisation sont si simples que les collaborateurs effectuent volontairement, volontiers et régulièrement la préparation du liquide de refroidissement. - Mais prenons les choses dans l'ordre.
Ce qui était autrefois mal aimé est aujourd'hui volontiers fait
La société kocher-plastik Maschinenbau GmbH est le leader incontesté du marché mondial des machines et installations qui, grâce à la technologie Blow-Fill-Seal (BFS), fabriquent en un cycle des systèmes pour le conditionnement de produits liquides et pâteux. Parmi les clients de cette entreprise traditionnelle de taille moyenne figurent les plus grandes entreprises de l'industrie pharmaceutique . Ce que Gerhard Hansen a fondé en 1963 s'est développé grâce à une croissance régulière et saine pour devenir une entreprise qui atteint constamment ses limites de capacité. L'agrandissement d'un hall pour augmenter la capacité fait déjà partie de la routine régulière à Sulzbach-Laufen.
Le taux d'intégration verticale pour la fabrication des machines et installations de remplissage à succès, qui jouissent du plus grand statut auprès des utilisateurs sous le nom de marque bottelpack®, est d'environ 70 %. L'entreprise fabrique exclusivement elle-même toutes les pièces importantes pour le système. Sur de nombreux centres d'usinage à quatre et cinq axes, elle fabrique des pièces de machines classiques ainsi que des moules pour les machines et installations modulaires et spécifiques aux clients. S'y ajoutent des tours, des perceuses et des rectifieuses pour d'autres processus d'usinage. "Plus de 20 machines sont réparties sur plusieurs halls", rapporte Bauer. Et toutes les machines sont approvisionnées en lubrifiant réfrigérant ou en huiles de coupe et huiles d'usinage. Chez kocher-plastik, on a renoncé à une installation centrale qui alimenterait toutes les machines. Bauer explique tout de suite pourquoi : "Le risque que toute la production s'arrête en cas de panne d'une installation d'alimentation centrale est trop grand pour nous".
Aspirer, nettoyer, repomper avec un chariot filtrant
Toutes les machines et tous les centres d'usinage ont donc leur "réservoir à bord". Celui-ci n'est pas toujours aussi facilement accessible que sur le BAZ Hermle que nous regardons en premier. Il suffit d'enlever le couvercle du réservoir librement accessible et les 1400 litres de réfrigérant lubrifiant sont facilement accessibles. Sur une ancienne fraiseuse Mazak, par exemple, le réservoir de liquide de refroidissement de 200 litres se trouve dans un bac sous la machine, accessible uniquement par un étroit caisson pouvant être couvert. Aspirer le liquide de refroidissement "usagé" et le pomper dans un bac mis à disposition, l'emporter ensuite pour traiter le liquide de refroidissement, le pomper dans un autre bac, puis le remplir à nouveau dans la machine, était autrefois une opération épuisante et quasiment sans fin. Les récipients de liquide de refroidissement devaient être nettoyés manuellement à l'aide de brosses. De plus, il était souvent difficile d'accéder aux réservoirs entre les machines très proches les unes des autres. "Les collaborateurs se sont souvent dérobés jusqu'à ce que cela ne puisse plus être repoussé", raconte Bauer. "Même s'ils savaient que cela n'était pas bon pour leur santé non plus".
Aujourd'hui, tout est beaucoup plus simple et les employés le font volontairement. Lorsqu'il est temps de préparer le liquide de refroidissement, le chariot d'aspiration et de filtrage SF500 de MKR Metzger, compact et maniable et très performant, est poussé à travers les couloirs étroits jusqu'à la machine. Dès que l'étroit accès au réservoir d'huile Mazak est dégagé, le tuyau d'aspiration de 4,5 m de long et de 50 mm de diamètre trouve une nourriture abondante. Un tuyau d'aspiration d'un peu moins d'un mètre de long avec une buse plate de 100 mm de large permet de travailler sans trop se baisser. Avec une puissance d'aspiration pouvant atteindre 250 l/min, le contenu est pompé hors de la machine et dans le réservoir de 500 l de la remorque d'aspiration . Le liquide passe alors à travers un filtre à bande sous vide. Les matières solides, les particules et les copeaux sont pris en charge par l'avaleur de copeaux intégré. "Avant, il était surtout très difficile de séparer les restes de l'usinage des matières plastiques", se souvient Dieter Geisßndörfer, qui utilise la Mazak. Après à peine trois minutes, le réservoir d'huile est vide et le filtre à bande ainsi que l'avaleur de copeaux sont pleins de copeaux et de particules. L'avaleur de copeaux se décroche comme un chariot dans le chariot et peut être facilement poussé sur des roulettes vers le lieu de recyclage des déchets. "C'est très pratique et ne demande pas beaucoup d'efforts", estime Geißendörfer, mais pas seulement.
Séparation efficace des huiles étrangères par le procédé de dérivation
Le réservoir d'émulsion est maintenant nettoyé à l'aide du système de nettoyage également présent sur le chariot filtre SF500 fonctionnement en dérivation. Via la lance haute pression, l'employé y injecte le liquide de refroidissement déjà nettoyé du camion-pompe avec une pression pouvant atteindre 70 bar. Cela permet d'éliminer même les résidus de saleté les plus tenaces. Ce fluide passe également une nouvelle fois à travers le filtre à bande avant que le liquide nettoyé et soigné ne soit repompé du réservoir du chariot d'aspiration dans la machine. Le chronomètre indique à peine douze minutes.
Bien que l'ensemble du processus de nettoyage, d'entretien et de préparation ne soit pas encore terminé, la machine peut déjà reprendre son travail. En effet, la séparation des huiles étrangères qui suit se déroule selon le procédé de dérivation pendant le fonctionnement de la machine. Pour cela, le séparateur d'huile étrangère TM450UV de MKR Metzger, également mobile, est poussé contre la machine et le flotteur avec support magnétique est plongé dans le liquide. La séparation de l'huile s'effectue selon le principe de coalescence . Les huiles étrangères qui surnagent sont retirées de la surface par le flotteur et acheminées en douceur vers un réservoir intermédiaire. Un paquet spécial de coalescence élimine les gouttes d'huile dispersées de l'émulsion . Celle-ci est à nouveau disponible pour le refroidissement dans son état de fraîcheur d'origine. Avant qu'elle ne soit renvoyée, les réacteurs UV à lit plat intégrés améliorent considérablement l'aspect et l'odeur des fluides de processus et suppriment efficacement la propagation des micro-organismes. Environ 27 minutes se sont écoulées depuis la première manipulation.
Production économique grâce aux chariots d'aspiration et de filtration
Bauer ne tarit pas d'éloges : "Nous sommes tous convaincus par la facilité d'utilisation, la rapidité de travail et les nombreuses solutions bien pensées des deux chariots de MKR Metzger". Les différentes mesures d'entretien et de préparation des fluides de process permettent de les garder performants plus longtemps. Cela se répercute sur la durée de vie des outils tout comme sur la précision de la fabrication. Chez Kocher-Plastik, la séparation régulière des particules, des copeaux et des huiles étrangères est désormais une étape importante vers une production hygiénique et économique. "Et cela fait aussi du bien à la santé de tous les collaborateurs", conclut Bauer.